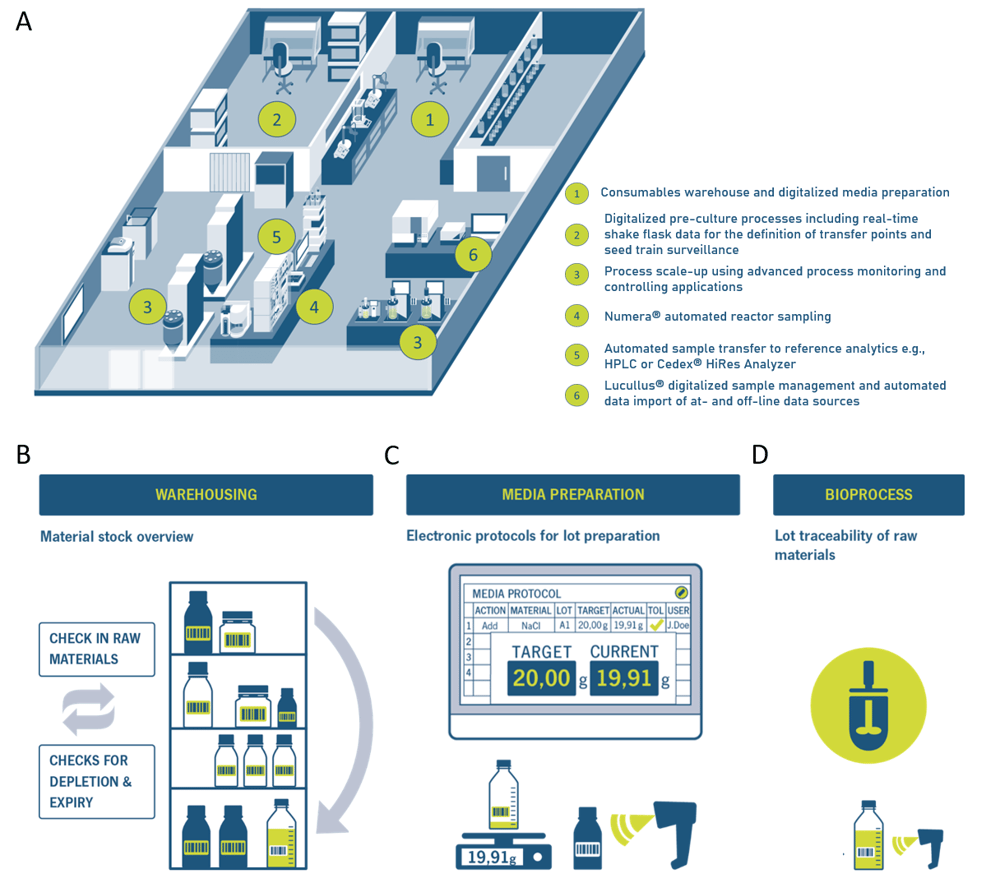
The i2BPLab (intelligent and integrated bioprocessing laboratory) at Zurich University of Applied Science (ZHAW) is funded by the Swiss government's Innosuisse Impulse Program (project number 41524.1 IP-ENG [5]) and aims to demonstrate how upstream unit operations in R&D labs and manufacturing plants can be successfully digitalized and automated to achieve paperless and more efficient workflows, embracing Bioprocessing 4.0 cornerstones (Figure 1A). The i2BPLab infrastructure is complemented by Securecell’s bioprocess digitalization and automation tools, Lucullus® and Numera®. With the modular sampling system Numera®, bioreactor sampling, sample processing, and transfer to an autosampler module for sample storage or to various 3rd party analyzers are completely automated. Lucullus® as overarching software monitors and controls all processes in up- and downstream over the complete seed train, including the bioreactor systems, the automated sampling system Numera® and integrated 3rd party analyzers.
However, Lucullus® is not only limited to basic SCADA (supervisory control and data acquisition) functionalities. Over the years, Lucullus® was extended by the Planning tool for bioprocess scheduling and preparation in terms of equipment assignments and sample planning, a Media Kitchen tool for raw material and recipe management, as well as guided media production, and the Graphic tool for advanced evaluation of process data and report creation. Thus, Lucullus® holds extensive and unique pre- and post-process running functionality.
Introduction
Bioprocessing 4.0 production concepts are defined as end-to-end digitally interconnected and automated bioprocess systems and additional equipment, forming the Industrial Internet of Things (IIoT). Such ideal production concepts run, monitor, control, and even improve the process via feedback loops and advanced mathematical modeling approaches. Bioprocessing 4.0 production concepts generate huge amounts of process data and thus heavily rely on efficient data management to allow real-time monitoring and process control [1,2].
Benefits of a digitalized pre-process phase
In many laboratories preparation of different consumables such as media, feeds, supplements, and buffers for upstream or downstream bioprocess applications is performed according to a printout protocol in a highly manual fashion. This entails a huge documentation and management effort of the warehouse, and in GMP (Good Manufacturing Practice) usually requires the four-eyes principle. Moreover, the manual preparation is error-prone, lot traceability is challenging, and lot quality variations of critical material attributes are even more difficult to identify. The aforementioned challenges of manual process preparation are effectively addressed by the Lucullus® Media Kitchen tool, digitalizing the process preparation phase to easily trace, document, and understand what happened before the bioprocess was started.
Figure 2: Top: Picture of the Media Kitchen setup in the i2BPLab at ZHAW. Within a small bench space, media management is fully digitalized. Bottom: Network diagram representing the Lucullus® Media Kitchen in the context of all Lucullus® integrated devices in the i2BPLab at ZHAW (for simplicity just a selection of integrated devices is shown).
Process flow Media Kitchen
The Media Kitchen tool has to be configured which is normally done by a Securecell employee according to customer requirements. The configuration includes the registration of integrated devices (e.g., pH meter, scales, label printer), the definition of possible actions (e.g., add material, start mixing, start incubating), the generation of a supplier catalog (e.g., Sigma-Aldrich, Thermo Fischer, Gibco), the listing of chemical groups (e.g., alcohols, ethers, thiols) just to mention a few. A proper configuration is important for the precise classification of the raw materials and the establishment of electronic protocols organized in action rows. After the configuration, all the raw materials are registered (Figure 1B), material details, supplier details, and lot number specified, and the respective barcodes printed. Also registered devices are labeled with a barcode. To create a new media lot, first, the device (e.g., scale) is scanned with a barcode scanner. Then, the raw material component is scanned, and the correct amount weighted. Lucullus® automatically takes the value of the scale and adds it to the respective action row of the protocol. If the weight-in value is not in a user-defined range, it will be rejected to avoid mistakes. Following this procedure, a new media lot can be prepared step-by-step just by scanning the barcodes and weighing raw material components (Figure 1C). The prepared consumables are then assigned to the respective bioprocess (Figure 1D). Following this procedure, full bioprocess information from the initial raw material lots to the final product is ensured.
Use-case: digitalized media management at ZHAW
The Lucullus® Media Kitchen tool is extensively used by members of the bioprocess technology group in the i2BPLab at ZHAW. Over 200 different consumables are registered in the digital warehouse and around 85 different protocols for media components or growth media are actively applied. At ZHAW, the Media Kitchen is composed of a balance, a pH meter, a label printer, and a barcode scanner (Figures 2). With as few as four devices and the software Lucullus®, media management is fully digitalized.
The Lucullus® Media Kitchen database is integrated together with upstream processing applications and analyzers via the local network in a central standalone Lucullus® installation. Each media, feed, supplement, and buffer produced can be assigned to the respective upstream processing application or analyzer with which it was used ensuring complete lot traceability.
Below the workflow of a guided LB-media lot creation using the Lucullus® Media Kitchen is described using screenshots, kindly provided by the members of the bioprocess technology group at ZHAW. From the media recipe database (Figure 3), listing all the historically produced media, feeds, supplements, and buffers, the corresponding consumable to be prepared (here LB-Fortified) is selected.
In the "New Lot" window (Figure 4), the lot name (here 220714_LB_Fortified_hatr) and amount (here 5 kg) need to be specified and the “Free Lot” checkbox unchecked. The checkbox can be activated, if the predefined concentration ranges of a raw material component in the electronic protocol is altered to perform DoE (Design of Experiment) for e.g., growth media optimization. Thus, the user is not forced to create several electronic protocols for the same consumable just differing in the concentration of one raw material component.
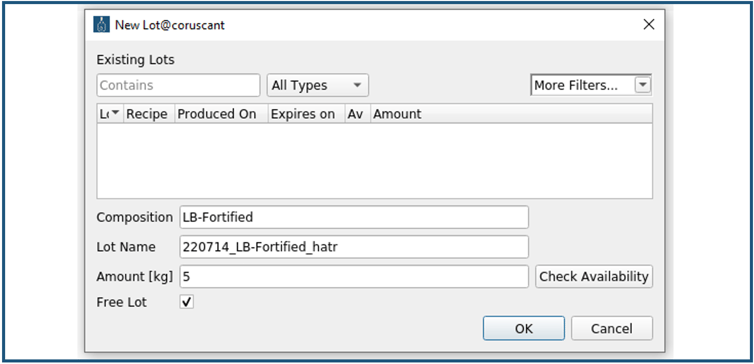
Thereafter, in the "New Lot" window, the “Check Availability” field is selected, and the "Available Ingredient Amounts" window opens (Figure 5). The availability of all raw material components that are needed to prepare the LB-medium is listed. If a raw material component is marked red, it is not available in a sufficient amount to produce the specified 5 kg of LB-medium.
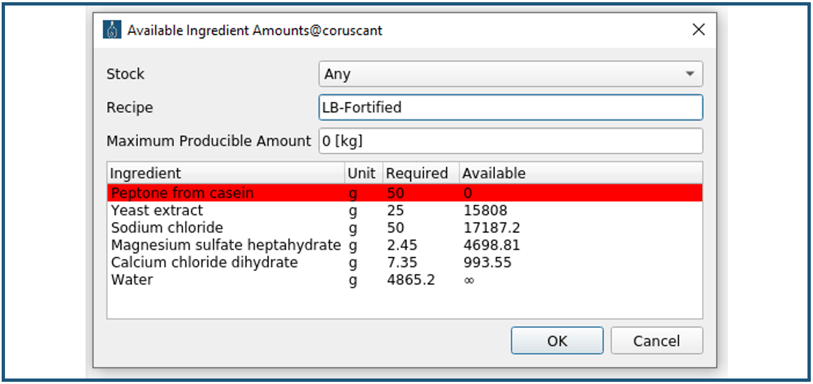
If all raw material components are available, the user can navigate to the guided media lot creation by clicking . The "Electronic Protocol" window opens (Figure 6) which is organized in action rows. Simply, by using the barcode scanner and weighing the correct amounts, the LB-medium is prepared step-by-step. If the actual raw material amount is outside a predefined range, the user cannot proceed to the next step in order to ensure maximum quality.
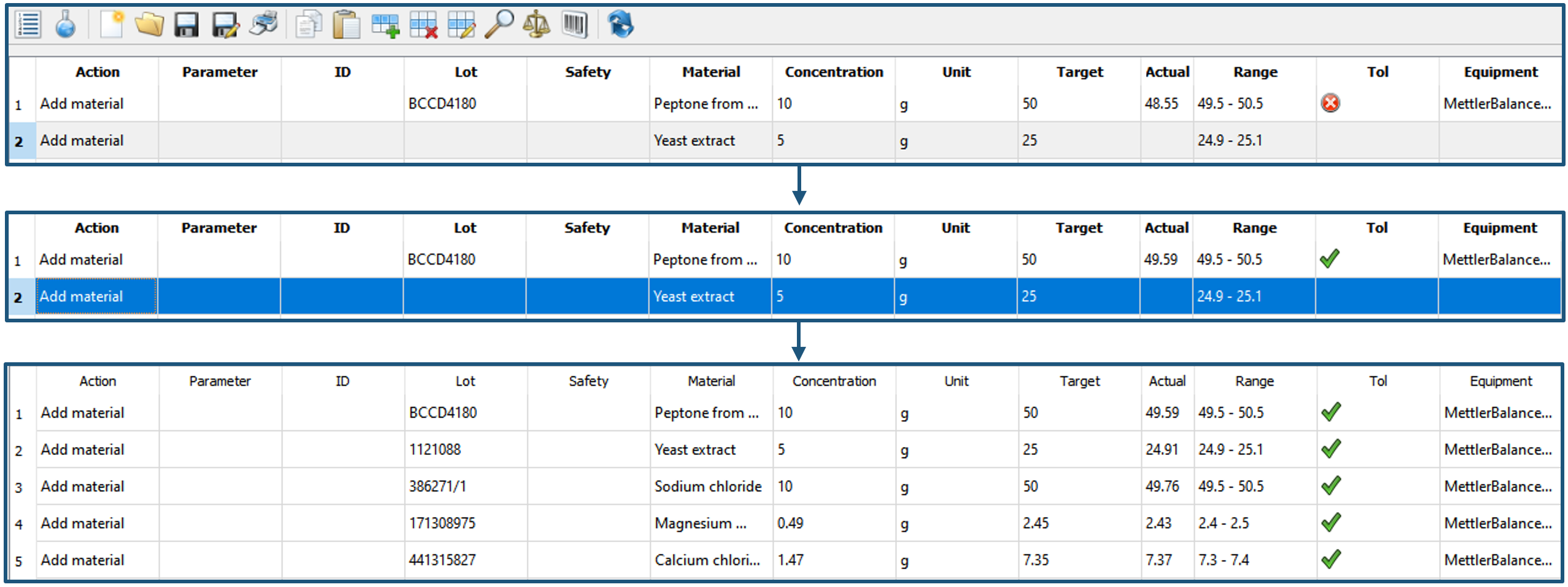
Before a process is started in the execution monitor, the prepared medium is assigned to the respective process to conveniently track the raw material footprint in the final product (Figure 7). In retrospect in the Evaluation tool, the user can search for all processes that were run with this lot of LB-Fortified medium.
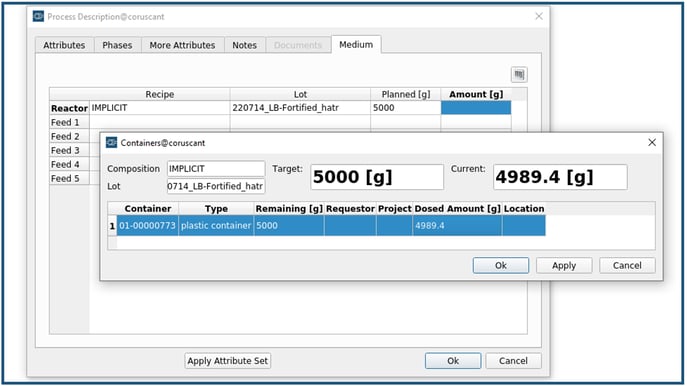
Conclusion
Compared to other industries, only a few R&D labs and manufacturing plants already comply with 4.0 production concepts. The i2BPLab at ZHAW showcases such a completely digitalized and automated innovation laboratory. Securecell’s bioprocess digitalization and automation tools Lucullus® and Numera® are integral parts of the i2BPLab infrastructure, contributing to paperless and more efficient workflows.
The use-case at ZHAW demonstrates the Lucullus® Media Kitchen as a valuable tool to completely digitalize the process preparation phase ensuring full data integrity from the initial raw material to the final product and thus closing existing gaps in the value chain of biotechnological products. Additionally, the Media Kitchen tool also facilitates media optimization and thus process optimization by conveniently tracking the raw material footprint in the final product. In the end, critical material attributes that influence critical quality attributes have to be understood and controlled and supplier/lot issues identified to ensure quality.
Key Findings: |
References
- https://www.pharmoutsourcing.com/Featured-Articles/568001-Bioprocessing-4-0-Where-Are-We-with-Smart-Manufacturing-in-2020/
- Scheper, T. et al. Digitalization and Bioprocessing: Promises and Challenges. in Digital Twins: Tools and Concepts for Smart Biomanufacturing (eds. Herwig, C., Pörtner, R. & Möller, J.) 57–69 (Springer International Publishing, 2021). doi:10.1007/10_2020_139
- Guidance for Industry PAT — A Framework for Innovative Pharmaceutical Development, Manufacturing, and Quality Assurance. Guidance for Industry. Accessed April 2022 download
- Sommeregger, W. et al. Quality by control: Towards model predictive control of mammalian cell culture bioprocesses. Biotechnology Journal 12, 1600546 (2017)
- https://www.aramis.admin.ch/Grunddaten/?ProjectID=45237